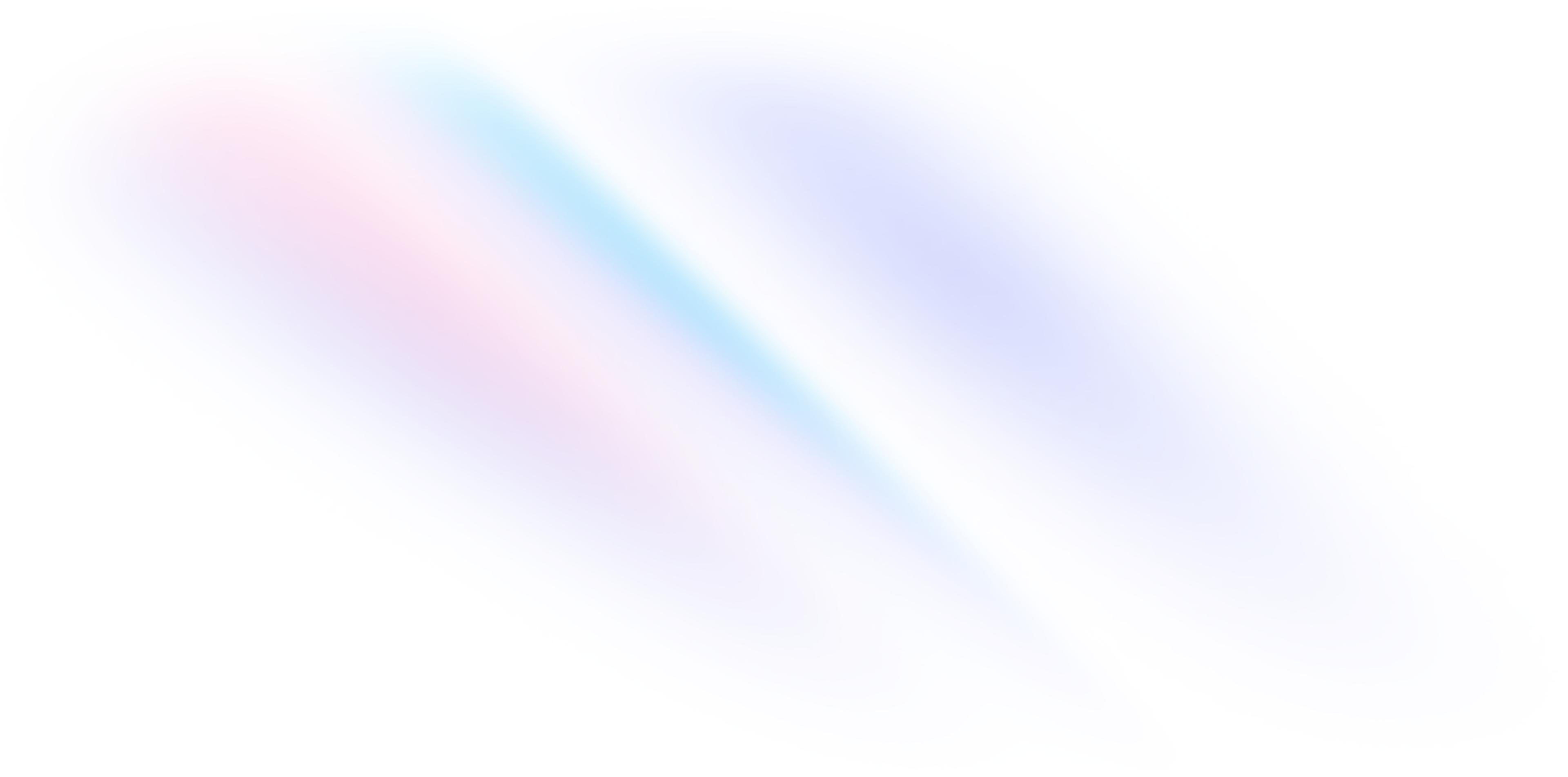
What strategies do Apparel Production Managers use to stay on budget?
1. Develop and Monitor Production Plans: An apparel production manager will create and monitor production plans which will help to ensure that all production activities remain within budget. This includes planning for labour costs, equipment costs, materials costs, and production times. 2. Analyze Costs and Negotiate with Suppliers: Apparel production managers analyze costs to determine where savings can be made. They also negotiate with suppliers to secure the best prices for materials and services. 3. Utilize Automation: Automation can help to reduce labour costs and increase production efficiency. Apparel production managers should research and invest in automated solutions that are cost-effective and will help to stay on budget. 4. Utilize Lean Manufacturing Principles: Lean manufacturing principles help to reduce waste and ensure that the production process is as efficient as possible. Apparel production managers should strive to implement lean principles to stay on budget. 5. Outsource Non-Core Activities: Apparel production managers may outsource certain activities that are not core to their business in order to reduce costs. This could include activities such as marketing or IT support.
Other Questions about Apparel Production Manager
- What is an Apparel Production Manager?
An Apparel Production Manager is responsible for overseeing all aspects of the production process for clothes and apparel. This includes managing staff, monitoring production processes, and working with designers to create new clothing lines. They may also be responsible for creating cost estimates, tracking inventory, and ensuring quality control standards are met.
- What experience is necessary to be an Apparel Production Manager?
Apparel Production Managers typically need a minimum of 3-5 years of experience in apparel production, manufacturing, or related industry experience. They should have a good working knowledge of production processes, quality control procedures, and garment manufacturing techniques. Experience with CAD, textile design software, and/or apparel design software is also beneficial. Knowledge of project management, budgeting, and scheduling are also important skills. Excellent communication, organizational, and problem-solving skills are essential.
- What are the typical duties of an Apparel Production Manager?
1. Develop and manage apparel production plans, schedules, and budgets. 2. Monitor production and quality control processes. 3. Hire, train, and manage staff to ensure efficient production. 4. Establish and communicate production goals. 5. Monitor labor costs and other related expenses. 6. Ensure production deadlines are met. 7. Liaise with designers, fabric suppliers, and other vendors to ensure materials and services are delivered on time. 8. Identify and troubleshoot production problems. 9. Prepare reports on production progress and related data. 10. Maintain records of production materials and processes.
- What sort of qualifications are required to be an Apparel Production Manager?
To become an Apparel Production Manager, you will need a minimum of a Bachelor's degree in a related field such as fashion design, apparel merchandising, textile science, or business administration. Additionally, you will need to have experience in the apparel industry and knowledge of apparel production processes. You may also need additional certifications or licenses, depending on the company or state you are working in.
- How much responsibility do Apparel Production Managers have?
Apparel Production Managers have a high level of responsibility. They are responsible for overseeing the day-to-day operations of the apparel production process, from the initial design stages to the final product. They are also responsible for setting budgets, scheduling production, managing personnel, monitoring quality control, and ensuring compliance with safety standards.
- What educational background is preferred for Apparel Production Managers?
Most employers prefer Apparel Production Managers to have a bachelor’s degree in a related field such as fashion design, merchandising, textiles, or business. Other helpful qualifications include experience in the apparel industry and knowledge of production processes. Many employers also prefer to hire candidates with knowledge of computer systems and software, such as Microsoft Excel.