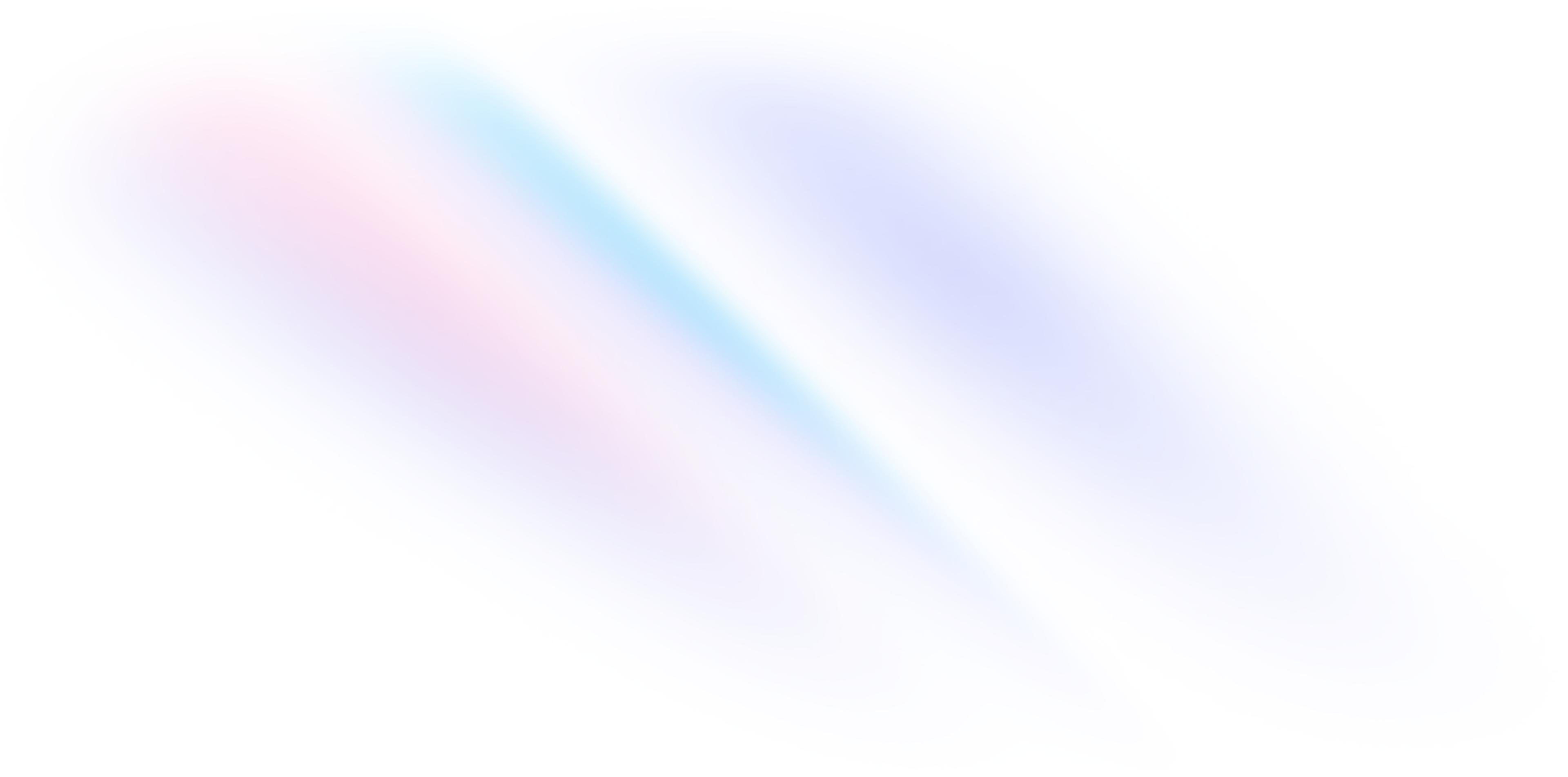
What is the typical work schedule for a Quality Control Coordinator?
The typical work schedule for a Quality Control Coordinator can vary depending on the specific needs of the organization they are working for. Generally, Quality Control Coordinators work full-time hours, typically 8-5, Monday through Friday, with some flexibility depending on the company's needs. Quality Control Coordinators may also be required to work additional hours, including evenings and weekends, depending on the demands of the job.
Other Questions about Quality Control Coordinator
- What is a Quality Control Coordinator?
A Quality Control Coordinator is a professional who ensures that a company's products and services meet the standards for quality established by the company and its customers. Quality Control Coordinators are responsible for developing and implementing quality control systems, conducting inspections, testing products, analyzing results, and creating reports. They also ensure that products comply with company and industry standards, as well as safety requirements, and may work with suppliers to ensure high-quality materials and components.
- What qualifications do I need to become a Quality Control Coordinator?
In order to become a Quality Control Coordinator, you will typically need a minimum of a bachelor’s degree in a field such as engineering, business, or a related field. You may also need experience in quality control and/or quality assurance. Additional certifications, such as a Certified Quality Engineer (CQE) or Certified Quality Auditor (CQA), may be beneficial. You may also need to be well-versed in the use of software and statistical analysis tools.
- What are the daily duties of a Quality Control Coordinator?
1. Monitor product quality throughout the manufacturing process. 2. Inspect incoming materials and components to ensure they meet quality standards. 3. Analyze production data to identify areas for improvement. 4. Develop and implement quality control procedures and systems. 5. Train personnel in quality control processes and procedures. 6. Investigate customer complaints and take corrective action where necessary. 7. Monitor compliance with applicable industry standards. 8. Create and maintain product quality records. 9. Ensure proper handling and storage of materials and finished products. 10. Prepare quality control reports and present findings to management.
- What type of training do Quality Control Coordinators receive?
Quality Control Coordinators typically receive training in quality assurance processes and methods, inspection techniques, and quality control standards. They may also receive training in data analysis, problem-solving, communication, and project management.
- What is the job outlook for Quality Control Coordinators?
The job outlook for Quality Control Coordinators is positive. According to the U.S. Bureau of Labor Statistics, the job outlook for Quality Control Coordinators is expected to grow 6% from 2019 to 2029. Quality Control Coordinators will be in demand as companies strive to meet quality assurance standards and regulations, and to ensure products are safe and of high quality.
- How much does a Quality Control Coordinator make?
Salaries for Quality Control Coordinators vary depending on experience, location, and industry, but according to Salary.com, the median salary for this position is around $68,310 per year.