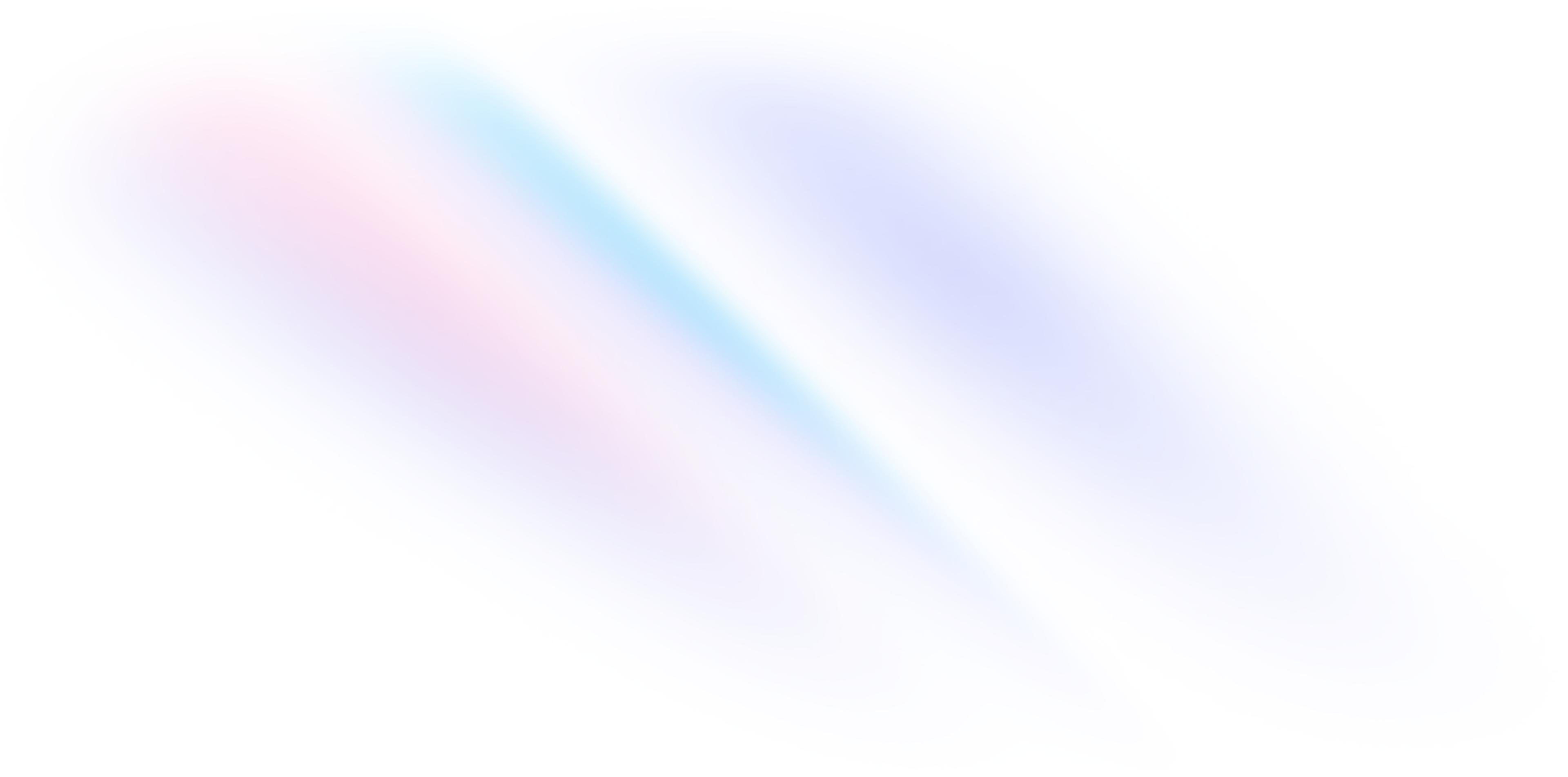
What are some common strategies for reducing product returns and improving reverse logistics processes?
1. Improve product descriptions and images to accurately represent the product. 2. Enhance quality control processes to reduce defective products. 3. Offer clear return policies and procedures to customers. 4. Implement efficient tracking and tracing systems for returns. 5. Optimize packaging to minimize damage during shipping. 6. Provide detailed installation or usage instructions to prevent customer errors. 7. Train customer service staff to handle return requests effectively. 8. Utilize technology such as artificial intelligence or machine learning to predict potential returns. 9. Partner with reliable and efficient shipping carriers. 10. Regularly analyze return data to identify patterns and address root causes.
Other Questions about Reverse Logistics Manager
- What is a Reverse Logistics Manager and what do they do?
A Reverse Logistics Manager is responsible for managing the reverse flow of products and materials from the customer back to the manufacturer or supplier. They oversee the entire process of returns, repairs, and recycling of products, ensuring efficiency and cost-effectiveness. This includes coordinating with various departments, tracking inventory, and implementing strategies to minimize returns and improve customer satisfaction. They also analyze data and identify areas for improvement in the reverse logistics process.
- What are the key responsibilities of a Reverse Logistics Manager?
A reverse logistics manager is responsible for managing the flow of products or materials from the end consumer back to the manufacturer or distributor. This includes overseeing product returns, refurbishment, and disposal processes as well as managing inventory levels and profitability. They are also responsible for implementing efficient and cost-effective reverse logistics strategies, maintaining relationships with vendors and customers, and ensuring compliance with regulations and sustainability practices.
- What skills and qualifications are necessary to become a successful Reverse Logistics Manager?
A successful Reverse Logistics Manager should possess strong analytical and problem-solving skills, as well as excellent communication and organizational abilities. They should also have a thorough understanding of supply chain management, inventory control, and customer service. Additionally, having knowledge of logistics software and experience in project management can be beneficial. A degree in business, logistics, or a related field, along with relevant work experience, is typically required for this role.
- What is the difference between traditional logistics and reverse logistics?
Traditional logistics refers to the process of planning, implementing, and controlling the flow of goods from the point of origin to the point of consumption. Reverse logistics, on the other hand, involves managing the flow of goods from the point of consumption back to the point of origin for the purpose of returns, repairs, recycling, or disposal. It is essentially the reverse of traditional logistics, with a focus on managing the flow of goods in the opposite direction.
- What are the main challenges faced by a Reverse Logistics Manager?
Some of the main challenges faced by a Reverse Logistics Manager include managing the flow of returned products, coordinating with multiple stakeholders such as suppliers, customers, and manufacturers, ensuring efficient and timely processing of returns, minimizing costs associated with returns, and maintaining visibility and control over the entire reverse logistics process. They also need to constantly adapt to changing regulations and technologies in the industry.
- What is the role of technology in reverse logistics management?
Technology plays a crucial role in reverse logistics management by facilitating the efficient and accurate tracking, processing, and handling of returned products. It enables the automation of key processes such as inventory management, product identification, and disposition, reducing the time and cost associated with returns. Additionally, technology allows for improved communication and collaboration between all parties involved in the reverse logistics process, leading to better customer satisfaction and increased profitability.